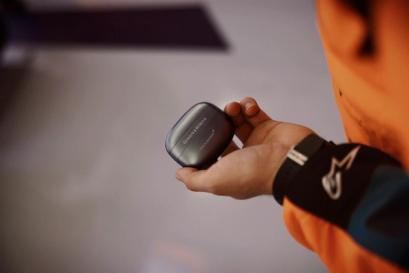
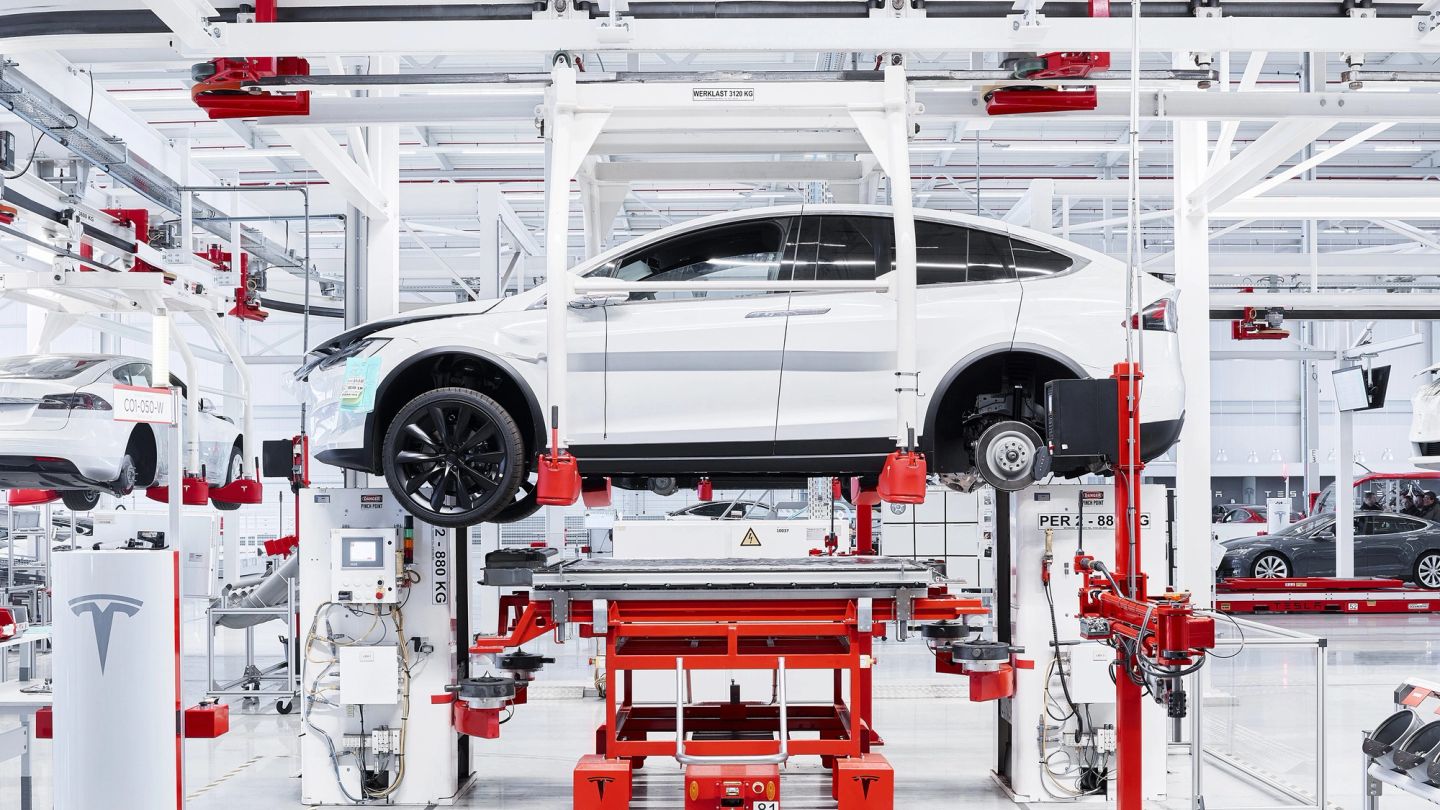
Leading the charge: Inside Tesla’s European mega-factory
Gentleman’s Journal head to The Netherlands to lift the lid on Elon Musk’s only base of operations outside the United States
Words: Jonathan Wells
Photography: Tom Bunning
Tesla, Elon Musk’s pioneering electric car company, is out of this world — and that’s no exaggeration.
Earlier this year, the entrepreneur launched his own cherry red Mark 1 Tesla Roadster into orbit, selecting it as the payload for the latest SpaceX rocket test. The car is still up there, a space-suited dummy sitting in the driver’s seat and David Bowie playing looped on the stereo. And so it shall remain. With half the solar system to cover, ‘Starman’ and his Roadster will stay in a state of constant punchline for hundreds of millions of years.
"Tesla, Elon Musk’s pioneering electric car company, is out of this world..."
It’s not the first time Tesla have come off as slightly alien. But, buy a Tesla in Europe today, and it comes not from beyond the stars, but from Tilburg — an industrial city two hours south of Amsterdam. This is the electric carmaker’s European factory, the brand’s only manufacturing complex outside of mainland America and their third largest overall. Let’s take a tour.
The ‘gliders’ first enter the factory...
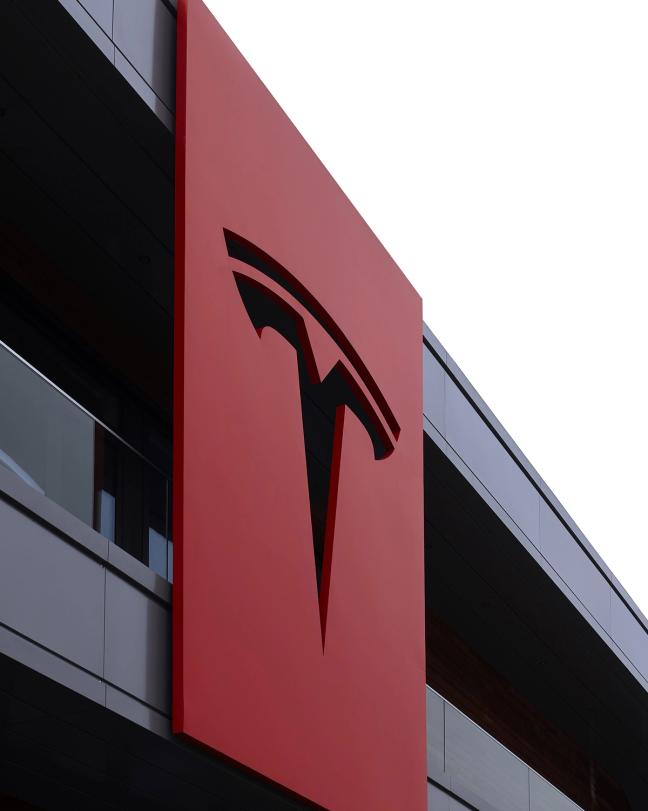
The Tilburg factory opened in 2015
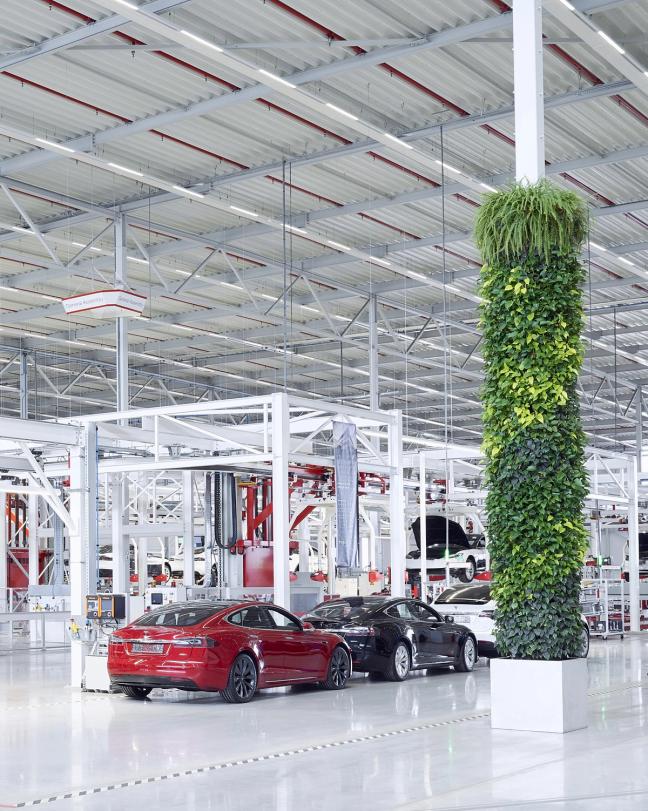
The ‘gliders’ are built in California
The Tilburg factory began assembling cars in 2015. Fast-forward three years, and 400 workers now ensure 120 cars roll of the production line every day. Easily accessible by river, rail and road, the factory is located for logistical purposes.
Shells of cars — nicknamed “gliders” — arrive at the complex in shipping containers. Built in Fremont, California, at Tesla’s second largest factory, these shells contain no engines or firmware. Instead, they contain a dummy subframe, which is removed when the car hits the assembly line.
The cars hit the assembly line...
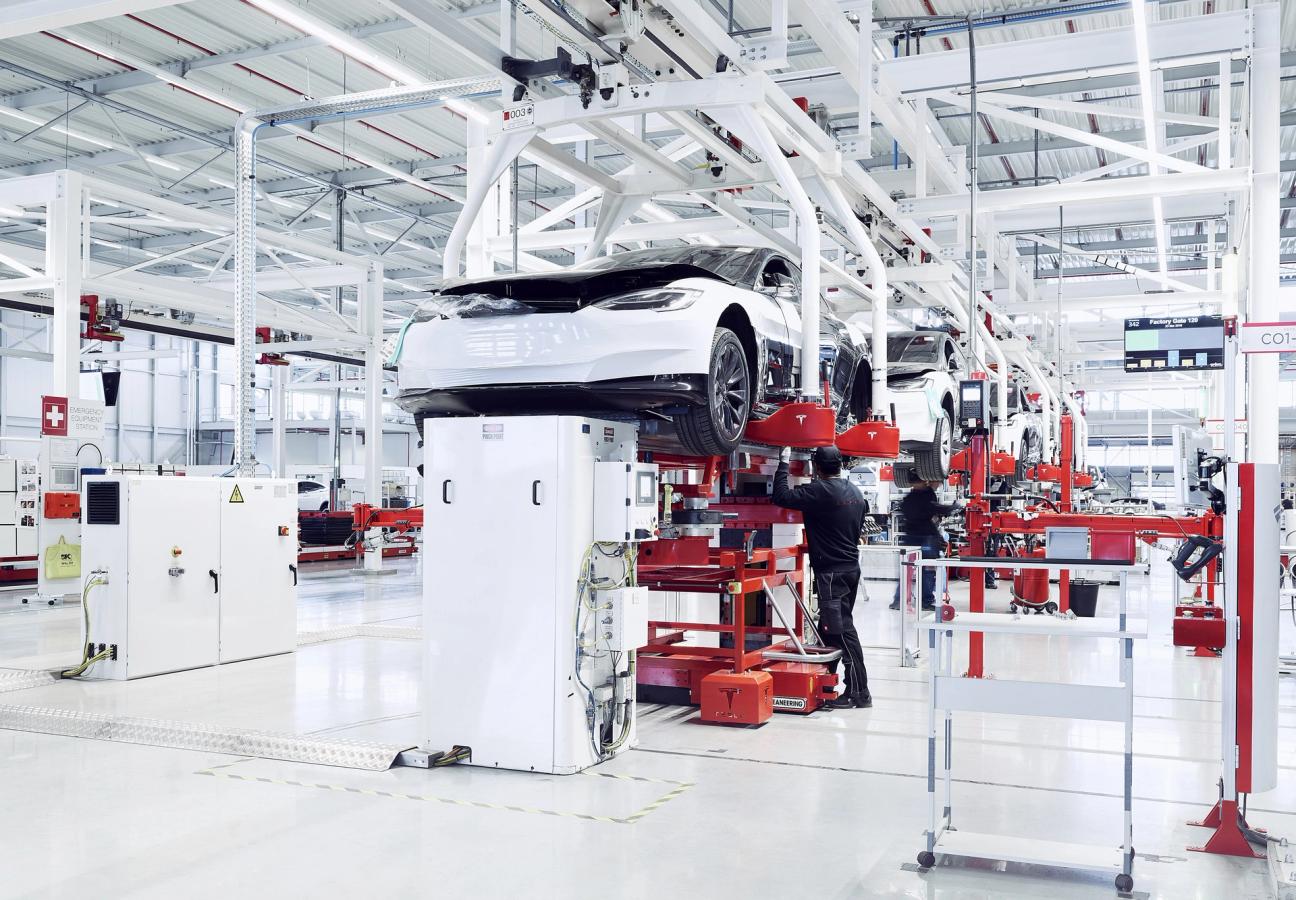
The rigs in this compartment were shipped from Fremont
The assembly line itself is the first of the factory’s four ‘compartments’ — meticulously-devised areas organised to ensure a smooth ride through the manufacturing process. The pristine white machinery of the assembly line, where the batteries and motors are fitted into the cars, were originally built for the Fremont factory, before being shipped over to Tilburg.
After the batteries and engines are in place (a Tesla electric engine is up to 57 per cent more efficient than an internal combustion engine), the firmware must be installed. A cable is temporarily connected to kickstart this upload, removed after just one minute when the network takes over and completes the process wirelessly. This is textbook Tesla: Simple, effective, effortless.
The cars have their software installed...

This is where the cars are first charged
Software comes next. The car rolls off the ramp and is bestowed with programming to control everything from the autopilot system to your personal media player. Sparked into life, the newly-talented Tesla is now charged.
After these charging capabilities have been assessed, the tests continue. The second ‘compartment’ is the testing area, where sensors, radar, cameras and wheel alignments are all put through their paces. But the most impressive calibration station is yet to come…
The cars take a dip in the water test...
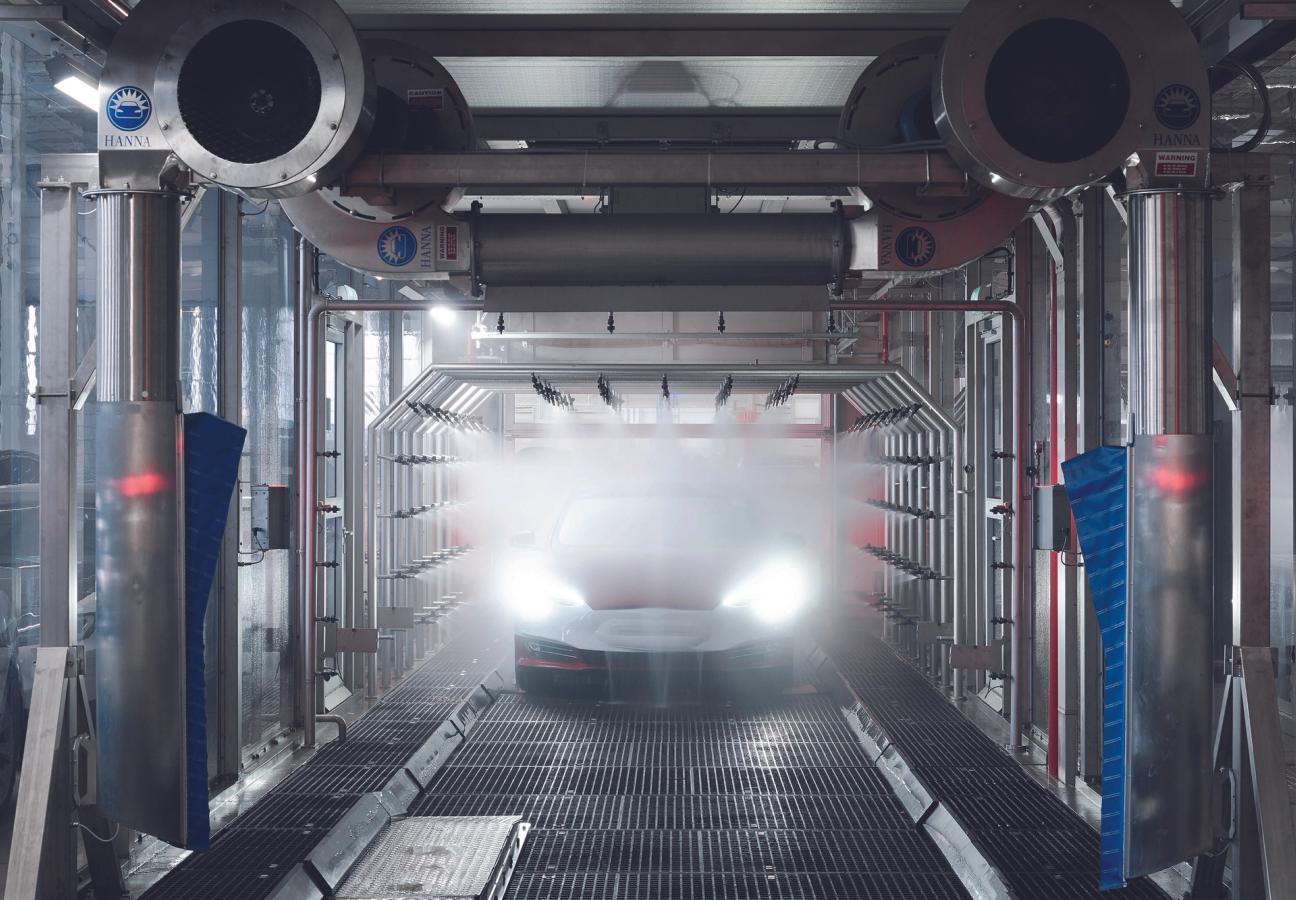
The water used in this compartment is 99.6 per cent recycled
Conceived to check the rubber seals of the cars, pressurised jets of water are powered at the vehicles. Tesla’s SUV effort, the Model X, is particularly scrutinised in this section, as its striking falcon doors and panoramic windshield means there is more rubber on show.
This water is 99.6 per cent recycled — just one of the factors behind the Tilburg factory’s exemplary BREEAM environmental and sustainability rating. Ranked in Europe’s top five, the complex’s eco-credentials were further boosted recently when the entire roof was fitted with solar panels.
Tesla's latest have a charge around the track...
Speaking of power, the third ‘compartment’ is the first opportunity the new cars get to really show what they can do. The test track, built entirely inside the factory thanks to Tesla’s zero emission machines, is 750 metres long — making it one of the longest indoor test tracks in Europe.
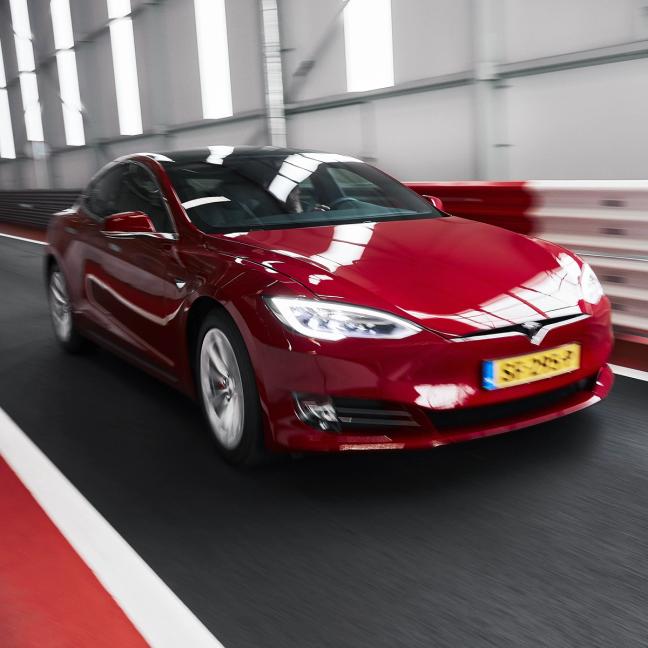
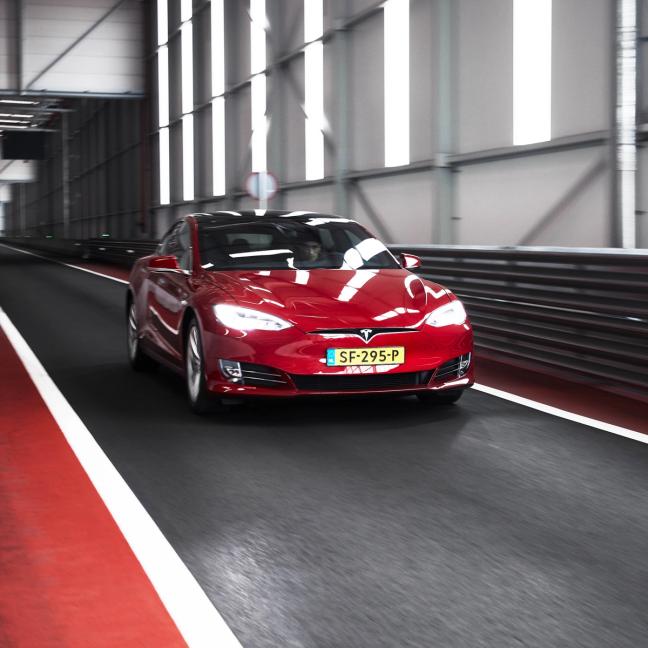
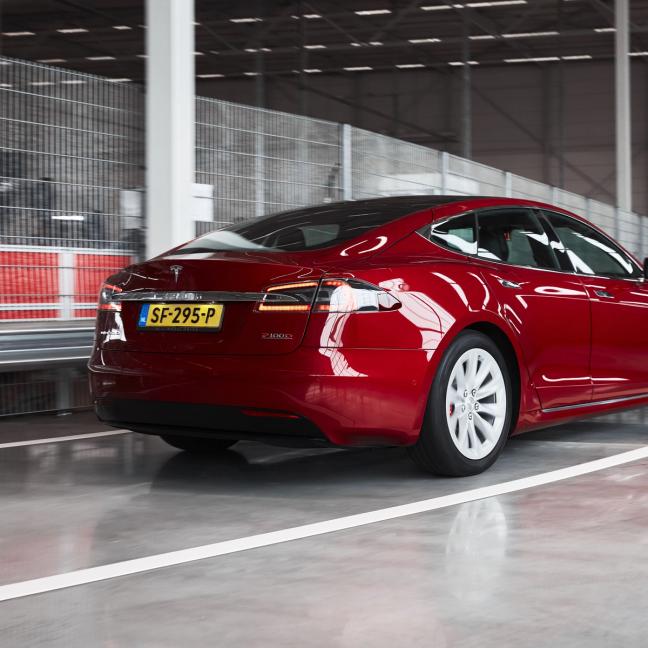
Specially-trained drivers test the cars across various sections of the track, which wends and winds its way through the entire factory and features ridges and bumps to simulate real road conditions.
The end is a light tunnel...
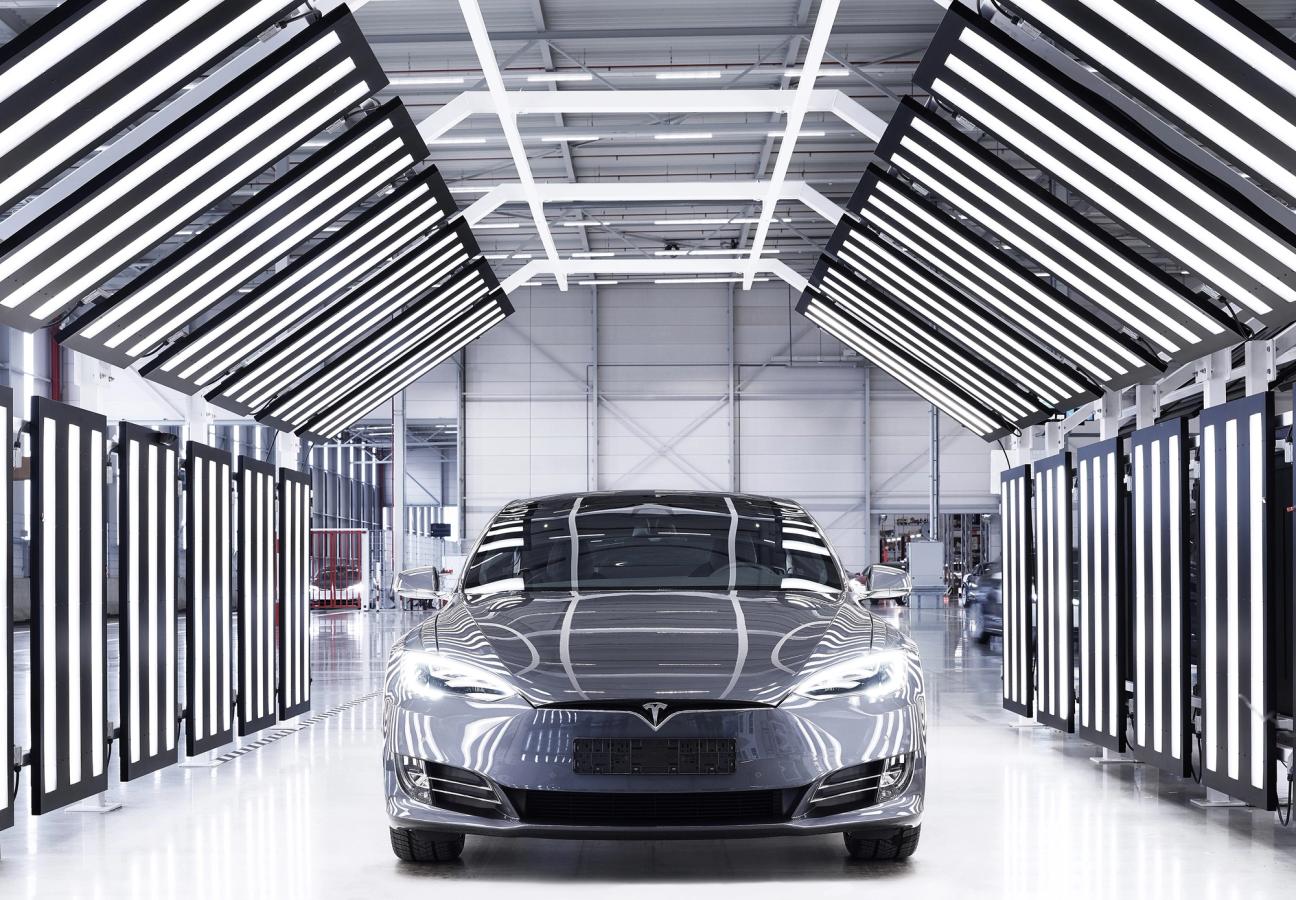
And finally, the cars undergo a full cosmetic check. This means driving into the light tunnel, an arch of full LEDs that emit a glow to show up any imperfections in the bodywork, rims and interior. It’s another almost ethereal part of the process, this final stage of production — and the light tunnel has a slightly spaceship-like quality to it.
But, unlike the cosmic convertible floating around in space, there is nothing otherworldly about these electric cars. They may seem alien, but this is thoroughly down-to-earth engineering. This is Tilburg. This is Tesla.
This article was taken from the May/June edition of Gentleman’s Journal. Subscribe here…